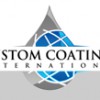
We apply advanced, high-quality coating solutions to treat metal parts, tools and components for oilfield, industrial, and manufacturing clients. Prevent flow plugging, friction, porosity, scale deposition, nuclei-site formation and enhance performance. Choose from: epoxy/ polyurethane systems, alkyd primer and topcoat systems, and under insulation (CUI) coatings.
Enhance performance and provide resistance to: erosion, wear, corrosion, abrasion and or heat. Boronizing base materials will give an extremely hard surface to increase the material's service life. Blasting is done before a protective coating is added to strip imperfections such as rust and other contaminants.
Enhance performance and provide resistance to: erosion, wear, corrosion, abrasion and or heat. Boronizing base materials will give an extremely hard surface to increase the material's service life. Blasting is done before a protective coating is added to strip imperfections such as rust and other contaminants.
Services
Custom Coatings International Inc. is located in Leduc, AB and was established in 2017. The company uses exclusive, high-quality coating solutions to treat metal parts, tools and components to help prevent corrosion, erosion and wear issues. These exclusive solutions and processes are directly related to the value and benefit of working with Custom Coatings International Inc.
We apply advanced, high-quality coating solutions to treat metal parts, tools and components for oilfield, industrial, and manufaturing clients. Polymer coatings such as Teflon can be used on carbon steel, aluminium, steel alloys, brass, magnesium, and stainless steel. Numerous coating choices exist, selecting the correct coating based on the operating environment is crucial to success.
The Pumpguard exclusive family of coatings is suited for all hostile environments and provides protection for service with scale deposition, nuclei-site formation, high build, dielectrics, volcanic, steam, geothermal, rubber, chemical environments and extreme wear conditions. We provide coating solutions for all wetted parts and completion tools.
Applying epoxies to pipe (spools) is the most common way of providing a barrier of protection to slow corrosion or prevent wear of the base material. Numerous internal coating choices exist, selecting the correct coating based on the operating environment is crucial to success. Let us help you choose the best option!
Tungsten Carbide coatings offer significant hardness, wear and corrosion resistance. The coatings are done through High-Velocity Oxygen Fuel spraying (HVOF) by using a combustive thermal spray at high velocity to develop a wear and corrosion-resistant coating.
This results in a very dense, very adhesive and cohesive tungsten carbide coating, with comparatively very high bond strength, low residual stress, low porosity (typically less than 0.5%), and high wear and corrosion resistance.This offers excellent corrosion resistance except in high pH environments and in hydrofluoric acid solutions.
This results in a very dense, very adhesive and cohesive tungsten carbide coating, with comparatively very high bond strength, low residual stress, low porosity (typically less than 0.5%), and high wear and corrosion resistance.This offers excellent corrosion resistance except in high pH environments and in hydrofluoric acid solutions.
Reviews
Be the first to review Custom Coatings International.
Write a Review